我国石油化工产业经济总量位居世界前列,但从整体来看仍然大而不强,其中炼油行业主要面临产能结构性过剩、成品油需求走势进一步分化、成品油质量升级和替代燃料发展迅速等问题;烯烃行业面临消费和需求增速放缓、竞争逐渐加剧、结构性短缺等挑战;对二甲苯目前缺口巨大,PX出口商较大程度上掌握着市场话语权,而我国目前已成为世界最大的PTA生产国,PX短缺导致整个产业链的利润受制于人,产业链风险凸显。未来几年我国石化工业急需转变增长方式,由产业大国向产业强国转型升级,重点做好6方面工作:优化布局,坚持一体化、集约化发展;优化烯烃原料结构,降低原油消费增长,提升成本竞争力;加强技术创新,加大催化柴油转化力度;高端化发展,补国内市场消费短板;加快淘汰落后产能,引导产业升级;适度放开成品油出口。
1我国石化产业现状及存在的主要问题
经过多年的快速发展,我国石油化工产业的经济总量已居世界前列,从2010年开始,我国已成为世界第一大化学品生产国和第二大石化产品生产国。2016年我国炼油能力约为7.94×108t/a,全年原油加工量为5.41×108t,炼油产能利用率不足70%,成品油产量为3.48×108t,成品油消费量为3.15×108t,净出口进一步增至3355×104t,消费柴汽比进一步降至1.37,柴油过剩严重,成品油出口(尤其是柴油出口)将呈现常态化和规模化的特点。受益于大量煤制烯烃(CTO)、甲醇制烯烃(MTO)、丙烷脱氢(PDH)装置的建成投产,烯烃尤其是丙烯能力快速增长,2016年乙烯和丙烯产能分别为2313×104t/a和3396×104t/a,原料多元化率分别为21.7%和38.4%,产量分别为2126×104t和2500×104t,当量自给率分别提高到了53%和77%。目前,国内多数石化产品产能过剩,但对二甲苯、乙二醇和苯乙烯等部分有机原料仍大量依赖进口,在高端及需要贴近市场提供技术服务的多元化、定制化领域,国内供给严重不足。近年,中东石化产品凭借价格优势,已经开始大量涌入中国市场,使得国内市场竞争进一步加剧。
1.1炼油
1.1.1产能大幅增长,结构性过剩问题逐渐显现
近年我国炼油行业快速发展。2010年,我国原油加工能力为5.48×108t/a,加工量为4.23×108t,三大类成品油产量2.53×108t,表观消费量2.45×108t。2016年,我国原油一次加工能力为7.94×104t/a,独立炼厂为申请进口原油使用资质共淘汰落后产能2933×104t/a,产能结构有所优化。2016年原油加工量为5.41×108t,燃料型企业和燃料—化工型(炼化一体化)企业平均开工率为71.3%,显著低于世界炼油平均水平(表1)。2016年成品油净出口量达到3356×104t,成品油出口(尤其是柴油出口)将呈现常态化和规模化的特点。
在原油一次加工能力总体过剩的同时,还存在着炼油能力两极分化的问题。
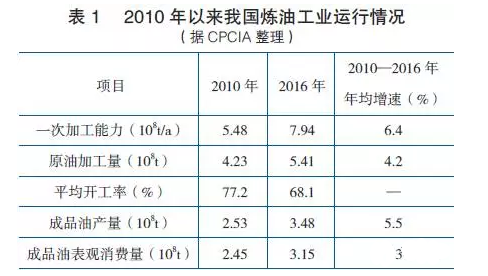
一是先进产能仍显不足。2012年全国炼油能力普查结果显示,单位能量因数能耗在8.5kg标油/t·因数及以下的炼油企业仅有中国石化广州分公司、中国石化镇海炼化分公司等13家企业,总原油一次加工能力仅为14950×104t/a,占全国总能力的18.8%。
二是存在大量规模小、技术水平低的落后产能,难以适应炼油产业集约化、规模化的发展要求。据中国石油和化学工业联合会(CPCIA)统计,截至2016年底,200×104t/a以下炼油厂共有68座,总能力仅为4781×104t/a,平均能力仅为70×104t/a,而大型炼厂也有一批落后的小装置。
三是炼化一体化水平有待进一步提高。目前我国24家千万吨级炼厂中仅有17家实现了炼化一体化,炼化一体化企业原油一次加工能力为23960×104t/a,占全国总能力的30.2%。
1.1.2成品油需求分化,产品结构调整压力较大
近年来,产业结构调整使得成品油消费结构发生了较大变化,突出表现在消费柴汽比大幅降低,已由2010年的2.18降至2015年的1.50,2016年柴汽比进一步降至1.37。未来柴油消费增长将大大慢于汽油,成品油需求分化趋势更加明显,预计到2020年消费柴汽比将大幅下降到1.1以下,而生产柴汽比降至1.18左右,未来柴油资源过剩加剧、汽油转为紧平衡。由此对炼油产品结构、装置结构调整提出了新要求,降低生产柴汽比任务艰巨(表2)。
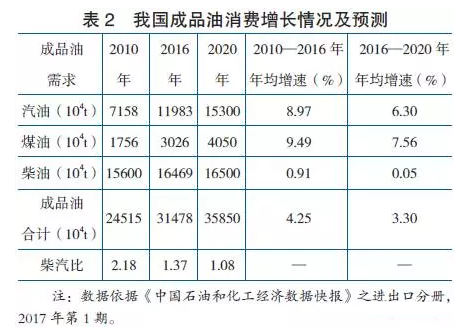
1.1.3未来炼油产能过剩形势依然严峻
2016年国内成品油需求量为3.15×108t,按照近年我国炼油行业成品油平均收率62%和合理开工率80%计算,合理配置炼油能力为6.35×108t/a,现有燃料型及燃料—化工型企业原油一次加工能力为7.59×108t/a,过剩达1.24×108t/a。
受我国经济增速放缓、结构调整稳步推进、传统产业深度调整等因素影响,“十三五”期间我国成品油需求增速将放缓至3%以下,预计2020年成品油需求将达到3.65×108t。根据目前各炼油企业在建、拟建和规划项目情况测算,并考虑淘汰落后,预计2020年国内原油一次加工能力将达到8.8×108t/a左右。按照62%的成品油收率和80%的开工率计算,2020年合理配置炼油能力为7.36×108t/a,届时过剩能力仍在1.4×108t/a左右,产能过剩形势依然严峻(表3)。
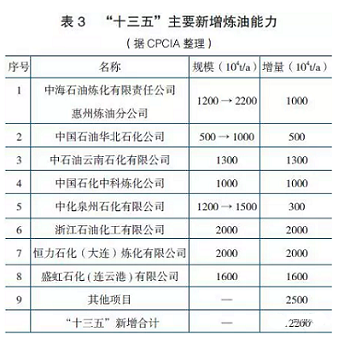
1.1.4成品油质量升级仍面临较大压力
为减少机动车排气污染,改善全国环境空气质量,有效治理雾霾,促进绿色发展和可持续发展,我国成品油质量升级继续加快,在“十三五”期间,2017年起车用汽柴油均升级达到国Ⅴ标准,2019年起达到国ⅥA阶段标准。截至2016年底,我国国Ⅴ汽油和柴油产能分别增长到了11477×104t/a和15303×104t/a;目前仅有中国石化燕山石化公司等少数企业可以生产国Ⅵ标准的汽柴油,国ⅥA汽油和柴油产能分别为355×104t/a和280×104t/a。因此为满足成品油质量升级的需要,我国炼油行业还需进一步完善装置配套,提升加工水平。
1.1.5国内外竞争加剧,市场化前景更加复杂
国内炼油产能总体过剩,行业内部竞争激烈,近几年来炼油开工率呈现明显下降态势。2010—2016年,原油加工量年均增幅仅为4.2%,全国炼厂开工率已由2010年的77.2%降至2016年的71.3%,地方炼厂平均开工率更是不足40%。
替代燃料发展迅速,挤压了成品油市场空间。中国替代燃料呈现多元化趋势,逐渐形成了以天然气为主,电动车、甲醇、生物燃料及煤制油等多种形式共同发展的格局。预计“十三五”期间,电动车将快速发展,替代燃料占成品油消费比重将从目前的接近6.5%上升至10.5%左右。
全球炼油产能重心东移,中国成品油出口竞争加剧。近年来,跨国石油公司加快在油气资源国和新兴市场布局大型炼油项目,中东部分资源国和印度大力发展外向型炼油产业,中国周边一些传统成品油进口国也在发展自己的炼油产业。中国成品油出口量大幅增加,将挤压传统成品油出口国的市场份额,未来东北亚成品油市场竞争将日趋激烈。同时,国内企业将承受更多成本价格的压力。
1.2烯烃
1.2.1产能保持稳步增长,原料多元化步伐加快
进入“十二五”以来,随着国内外经济和产业发展形势发生巨大变化,我国烯烃行业竞争格局也发生转变,进入结构调整阶段,其突出特点是行业发展重心从单纯追求规模化发展向追求提升综合竞争力转变,生产和消费增速明显放缓,原料结构调整和产品结构升级成为主要发展趋势。
2016年我国乙烯能力增至2304×104t/a,新增产能全部来自煤制烯烃、甲醇制烯烃,产量达2171×104t,当量自给率增至52.5%;2016年我国丙烯能力增至3339×104t,产量达2542×104t,当量自给率增至75.2%(表4)。
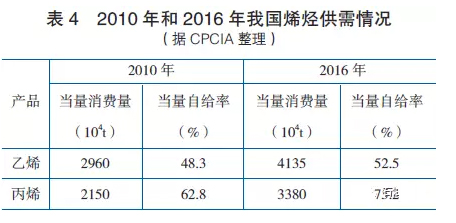
我国已在世界范围内率先实现了煤制烯烃产业化,在高油价条件下,煤制烯烃、甲醇制烯烃与石脑油蒸汽裂解工艺相比,具有明显的成本优势,在“十二五”期间发展迅速,截至2016年底,国内已有11套煤制烯烃、16套甲醇制烯烃、11套丙烷脱氢(含2套混合脱氢)装置投入产业化运营,合计总烯烃能力1759×104t/a,占到国内乙烯总能力的21.7%、丙烯能力的38.4%。但自2014年下半年以来,国际油价呈现断崖式下跌,使得煤制烯烃、甲醇制烯烃相对传统石脑油蒸汽裂解路线的成本优势显著下降。预计“十三五”期间,国际油价将主要在45~70美元/bbl区间运行,煤制烯烃、甲醇制烯烃仍有发展机会,但竞争优势不再明显,应科学规划、合理布局、适度发展。
1.2.2消费和需求增长速度逐步放缓
2010年以来,由于经济增速下滑导致下游需求不旺,国内乙烯、丙烯需求增速明显放缓,2016年国内乙烯、丙烯表观消费量分别约为2335×104t和2832×104t,考虑到下游产品的净进口,乙烯、丙烯当量消费量(国内产量+进口量-出口量+下游产品净进口的折合)分别约为4135×104t和3380×104t,2010—2016年期间国内乙烯、丙烯当量消费量年均增速分别为5.7%和7.8%。
预计未来几年我国经济增速将进一步回落,对乙烯、丙烯下游产品需求增速将放缓。根据对乙烯、丙烯下游产业发展预测,预计2020年国内乙烯当量需求量将增长到4800×104t左右,2016—2020年间年均需求增长率约为3.8%;到2020年国内丙烯当量需求量将增长到3900×104t左右,2016—2020年间年均需求增长率约为3.6%(表5)。
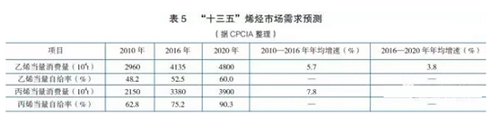
1.2.3烃行业竞争逐渐加剧,竞争态势日益复杂
我国是世界上最重要的石化产品市场之一,虽然国内烯烃当量需求量仍将保持增长,但是从世界范围看,竞争程度更加剧烈,竞争态势更加复杂,中国则是各生产商激烈争夺的主要市场。未来我国烯烃产业首先面临着中东、北美低成本产品的竞争,又面临着欧美、日本、韩国等高端产品的竞争(表6)。在我国行业内部,由于多元化原料烯烃生产的快速发展,不同原料路线烯烃生产的竞争态势也更加明显。
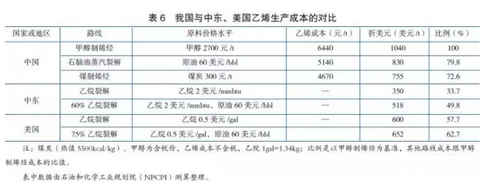
目前,中东地区乙烯装置所用乙烷原料价格普遍为2美元/mmbtu(百万英热单位)左右,折合约100美元/t,据此推算其乙烯生产成本仅为350美元/t左右,为中国烯烃生产成本的34%~46%。即使按照60%乙烷+40%石脑油计,其乙烯生产成本为517美元/t,仍比我国低30%以上,成本优势非常明显。近年来中东石化产品凭借价格优势,已经开始大量涌入中国市场。2015年和2016年,我国进口聚乙烯和乙二醇中超过50%来自中东地区。预计在2020年之前,我国将面临中东低成本大宗石化产品进口的持续压力。中东地区产业快速发展对国内市场的冲击已逐步显现。
1.2.4国内石化产品供给存在结构性短缺
我国部分基础石化产品(特别是以石油为原料的产品)对外依存度较高。2016年乙烯(当量)、对二甲苯、聚乙烯、乙二醇、苯乙烯的自给率分别为52.5%、43%、62.9%、34.6%和60%。究其原因:一是我国石油短缺,用于生产乙烯、芳烃的石脑油资源供应紧缺;二是与中东、北美廉价的乙烷原料路线乙烯相比,石脑油路线成本高、竞争力弱;三是受近期石化产品整体市场低迷以及社会舆论压力的影响,大型石化项目建设进度延缓(表7)。
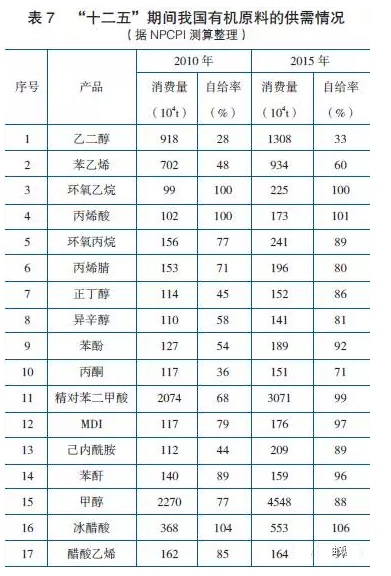
高技术含量的化工新材料和高端专用化学品国内自给率偏低,工程塑料、高端聚烯烃塑料、特种橡胶、电子化学品等高端产品仍需大量进口。比如,聚碳酸酯近年国内缺口一直在100×104t以上;聚酰亚胺、聚芳酯、全氟橡胶等位于“新材料金字塔”顶端的特种高端材料,国内生产长期处于空白。而部分化工新材料在技术来源获得突破后,产能迅猛增加,但由于所获技术属于国际低端水平,产品档次低,品种牌号少,只能满足低端市场需求,或者技术不成熟,运行不稳定,市场竞争力差,从而出现了国内自给率和装置开工率“双低”的现象,比较突出的有碳纤维、聚甲醛、聚四氟乙烯等。
1.3对二甲苯
1.3.1产业规模持续增长,投资主体多元化发展
近年来我国对二甲苯(PX)总产能和平均规模逐年增长。2016年,我国共有PX生产企业17家、装置23套,合计PX产能达到1368.7×104t/a,企业平均规模达到80.5×104t/a,装置平均规模达到59.5×104t/a,均已高于世界平均水平。近年来我国PX装置大型化趋势明显,新建PX装置规模均在60×104t/a以上,单套最大规模已达到160×104t/a。
近年来由于中国石油、中国石化两大集团以外的企业特别是部分外资和民营资本的进入,行业投资主体呈现多元化发展趋势,行业集中度有所下降。2000—2016年期间,国内PX生产企业从7家上升至17家,前4位企业产能占比从85.8%下降至30.7%;目前非两大集团的PX产能占总产能的47.1%,较2000年有了较大增幅(表8)。
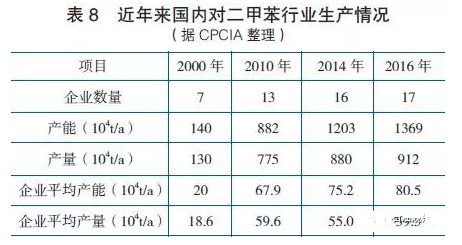
1.3.2市场供需矛盾突出,但未来几年缺口将大幅缩小
2015年,我国对二甲苯产量为912×104t,净进口量为1152.9×104t,表观消费量约为2068×104t,自给率仅为44.3%。2016年国内对二甲苯产量为956×104t,较上年提高4.5%,但下游精对苯二甲酸(PTA)需求增长更快,PX供需缺口继续扩大,2016年对二甲苯净进口量达到1230×104t,自给率将进一步下降到43.7%。
近年来由于国内聚酯行业快速发展,大量聚对苯二甲酸乙二醇酯(PET)和PTA产能的释放,拉动了PX市场需求的高速增长,2005—2016年期间国内PX表观消费量年均增长速率高达18%,远高于乙烯、丙烯、苯等其他大宗基础有机原料;而同期受原料供应以及PX项目群体性事件频发等多重因素影响,产能、产量增长滞后,导致国内供需缺口从2005年的154.5×104t大幅增长到2016年的1230×104t,2005—2016年期间年均增长速率高达20.5%,国内自给率从2005年的59.1%下降到2016年的43.7%。
PX作为未来较长时间内国内少数缺口较大的有机化工产品之一,企业投资建设的积极性较高。且随着PX产业准入门槛的降低,未来只要有原料资源、与下游产业相匹配、进入国家七大石化产业园区、能耗指标先进的装置都可能如期建成,届时PX供需缺口将大幅度缩小。预计2020年国内PX净进口量将缩小到500×104t以下。
1.3.3原料结构优化空间依然较大,炼化一体化水平仍待提升
随着国内炼油产能的持续增长,特别是一批千万吨级大型炼化一体化项目的实施,我国PX原料结构得到了明显改善,但依然存在较大优化空间。国内许多大型炼化一体化项目在油品—乙烯—芳烃生产之间的关系不能充分优化,油小化大,炼油能力及二次加工方案不能与下游乙烯、芳烃生产充分匹配,导致经常出现乙烯、芳烃争原料的现象,为了保障乙烯原料供应,国内芳烃原料经常供应不足,影响PX装置开工率;另外,由于PX生产装置的主要原料之一是重整装置生产的重整生成油,其也是重要的高辛烷值汽油添加组分,随着国内汽车工业的大发展,汽油的需求量也日益增加,更加大了PX原料供应紧张程度。因此,应通过炼化一体化优化,适当扩大配套炼厂加工能力,优化装置配置并合理调整加工流程,根据市场需要和价值规律,灵活安排芳烃—乙烯—汽油生产的关系,增强竞争力,实行炼化一体化企业利益总体最大化。同时,积极拓展凝析油、甲醇等其他原料的使用,同时结合柴油加氢裂化等新技术,逐步解决原料资源紧张的局势。
2石化工业结构优化建议
2.1坚持一体化、集约化发展,优化布局
统筹炼油能力发展与烯烃、PX项目建设,尽量依托现有企业,在少增或不增炼油能力的条件下新建、扩建乙烯和PX装置,进一步提高炼化一体化水平,缓解油品区域过剩矛盾。
一是要推动具有竞争优势和发展潜力的现有企业实施炼化一体化改造,建设中国石化九江石化芳烃项目、广西石化芳烃工程、海南炼化一体化改扩建工程、泉州石化一体化改扩建工程、镇海炼化一体化改扩建工程等。
二是要支持区域资源集约化、一体化,采取跨地区、跨所有制和企业联合布局方式,集中分散的化工轻油和芳烃资源,布局大型乙烯和PX项目,建设中国化工(山东)百万吨乙烯工程、山东东营港经济开发区芳烃项目、河北玖瑞化工芳烃工程等。
2.2优化烯烃原料结构,降低原油消费增长,提升成本竞争力
我国烯烃工业优化原料结构主要立足以下几个方面:一是考虑综合效益,成品油供应过剩,尤其是柴油过剩压力较大地区的炼化一体化企业,可适度提高裂解装置原料中轻柴油比例。2016年我国裂解装置原料结构中,轻柴油占比约8%,若将轻柴油占比进一步提高到15%,可化解炼油能力900×104t/a。
二是深入挖掘传统石脑油蒸汽裂解制乙烯路线资源一体化利用潜力。通过优化炼化一体化方案,合理配置炼化一体化项目的原油加工能力和加工方案,优化全厂物料平衡,并充分考虑区域内油田、炼厂等其他渠道的资源统筹利用,尽量减少石脑油在乙烯原料中所占比例,加大轻质化原料和低品位原料如炼厂轻烃、油田轻烃、凝析油、各类回收气等的利用程度。
三是大力推广催化干气回收乙烯、裂解汽油回收苯乙烯等新技术,提高现有资源的利用品位,实现有限资源条件下的最优化利用。
四是积极布局海外轻质化原料资源,包括中东轻烃及凝析油、北美页岩气及其伴生乙烷、丙烷等,探索依托这些资源在国内或海外发展乙烷、轻烃裂解制乙烯、甲醇制烯烃或丙烷脱氢的可行性。
2.3加强技术创新,加大催化柴油转化力度
目前,全国催化能力为2.32×108t/a左右,催化柴油产量约为3700×104t/a,这部分催化柴油硫含量高、十六烷值低、多环芳烃含量高,是制约柴油升级的主要瓶颈。大力开发和应用催化柴油转化技术,不断提高催化柴油转化技术的效能,降低能耗和氢耗,将催化柴油组分转化为汽油组分和轻质芳烃,不但有利于柴油质量升级,而且可以降低柴汽比。
2.4高端化发展,补国内市场消费短板
未来中国烯烃工业产品结构升级的主要方向是差异化、高端化发展,具体而言:对于传统石脑油蒸汽裂解制乙烯装置,调整方向主要是利用国外乙烯原料轻质化带来的差异化发展机会,充分发挥液体原料(主要是石脑油)蒸汽裂解装置产品结构丰富的特色,走C2、C3、C4烯烃及芳烃耦合发展路线,并挖掘C4、C5、C9等副产品深度加工的增值潜力,将其转化为乙烯装置下游产业链综合发展优势,丰富产品结构、提升产品附加价值,实现与乙烷裂解、MTO、PDH等路线的差异化竞争。同时在终端产品定位上,加大高技术含量、高附加值的化工新材料、专用化学品的比例,探索高端化发展路线。通过产品结构多元化、高端化、差异化调整,以产品附加值提升弥补成本劣势,并进行差异化竞争。
2.5加快淘汰落后产能,化解产能过剩,引导产业升级
通过制订炼油行业装置能耗、物耗、安全、环保、油品质量等方面的先进标准、准入标准和落后标准,并严格监督执行,引导行业转型升级。对于运行情况处于落后产能标准的炼油企业,建立产能淘汰和置换政策,发挥市场配置资源的决定性作用,结合《关于进口原油使用管理有关问题的通知》(发改运行[2015]253号),淘汰一批产品质量低劣、能耗高、资源利用不合理、安全隐患较大及环保不能达标的炼油装置,为先进产能腾出发展空间。
结合“新常态”,优化项目建设方案和建设节奏,一些炼油企业已主动采取措施,取消了一些改、扩建项目,适当推迟了部分项目的建成投产时间,在条件具备的基础上再适时启动。鼓励企业通过资本运作、兼并重组、关停并转等方式逐步化解产能过剩。
根据目前独立炼厂申请进口原油使用资质申报情况,预计“十三五”期间还可淘汰落后炼油能力3000×104t/a以上。
2.6适度放开成品油出口
随着国内炼油能力进一步增大,产能一直保持较高的过剩,今后成品油出口将是保持国内市场平衡的重要手段,中国的成品油出口量可能大幅提升,出口压力突出。同时,由于我国柴油消费增长缓慢,汽油需求增长仍然强劲,柴汽消费比下降,因此,在保证国内汽油供应的同时,柴油过剩倾向更为明确,预计柴油出口压力会更大。
为此,适度放开成品油出口贸易,在保障国内成品油需求的前提下,通过进出口调节供需结构,鼓励国内企业积极开拓国际市场,尤其亚太地区印度尼西亚、马来西亚、菲律宾、越南和澳大利亚等周边地区市场。